
Want to introduce your team to 5S?
Long considered a foundation of high performing organisations, 5S is a simple and accessible technique that provides immediate and significant benefits by de-cluttering workplaces and providing a framework for maintaining high standards of housekeeping and organisation. This workshop provides participants with the tools and knowledge to enable them to implement 5S in their workplaces.
About our 5S Training Workshops
In this video, Chris Baker, founder and principal business advisor at Kallista Consulting, talks about how our 5S Training Workshops can help to transform your organisation’s housekeeping and layout standards driving increased productivity and building a foundation for further improvement.
5S is Fundamental to Productivity
Improved Productivity
5S delivers productivity by ensuring that work areas are properly equipped with just the tools and equipment that they need to function. Once the clutter is removed and everything has a home in a sensible place, teams are able to quickly locate what they need as they transition from task to task, reducing changeover and cycle time.
Reduce Safety Hazards
By reducing clutter, improving cleanliness, and optimising workplace layout, the risk of slips, trips and falls is reduced and work areas can become safer places for employees. The 5S methodology increases the sense of ownership of the workplace amongst employees, leading them to take better care of it and make sures the rules are followed.
Better Quality & less Waste
Standardisation and visual controls lead to improved adherence to procedure, resulting in more consistency in finished product. Greater consistency means fewer rejects and less wasted time and material.
But there are things that get in the way….
5S does not come naturally. Most workplaces we encounter that don’t already have an established 5S program exhibit large amounts of clutter, poorly laid out workstations and excessive waste as employees search for tools and materials or move longer than necessary distances.
While none of the concepts of 5S are particularly complex, in the absence of a formal structure and a shared knowledge of what is required, teams rarely achieve a high standard without practical training and a good implementation framework.
How we can help
Having completed this course, participants will understand:
the meaning and application of the processes associated with 5S (Sort, Set In Order, Shine, Standardise and Sustain),
how to objectively score an area for 5S compliance and identify improvements,
how to use 5S tags and a 5S holding area,
how to improve process through appropriate layout and storage of tools and raw materials,
how to use colours and standard signage to improve productivity and how to work as part of a team at toolbox meetings to identify improvements and solve problems
So why not talk to us now so that we can design a program that helps you meet your Introduction to 5S goals ?
Pricing
-
In House Workshops (Highly Recommended)
Our industry expert comes to your premises and facilitates the training.
One day on-site Workshop - from $2800 to $4800 (depending on numbers and location)
Two on-site one day Workshops
Our recommended approach is two site visits separated by an interval as your team begins implementation.
from $4800 to $6800 (depending on numbers and location)
(Volume Discounts apply - Contact us for a quote)
-
Live On-Line Workshops
Our facilitator delivers two interactive 3hr workshops to a remote audience via teleconference. Each workshop is separated by an interval of several weeks to allow participants time to begin implementation
From $2800 for 10 participants
-
Online Self Paced Learning
from $395 per person
(Volume Discounts apply - Contact us for a quote)
What People Are Saying
“I love the flexibility in the approach that Kallista Consulting takes to tailor a program to meet our specific business challenges. In addition, the energy and personal commitment the team takes to deliver the best-in-class learning experience”
Bobby Pavlickovski
Director Operations | Thales Australia
“Having worked with Kallista Consulting for more than 10-years now, Entegra have found Chris an excellent resource to align with for implementing process performance, systems & structure, driving a culture of continuous improvement and developing emerging leaders amongst our organisation.”
Laurie McCalman
Managing Director | Entegra Signature Structures
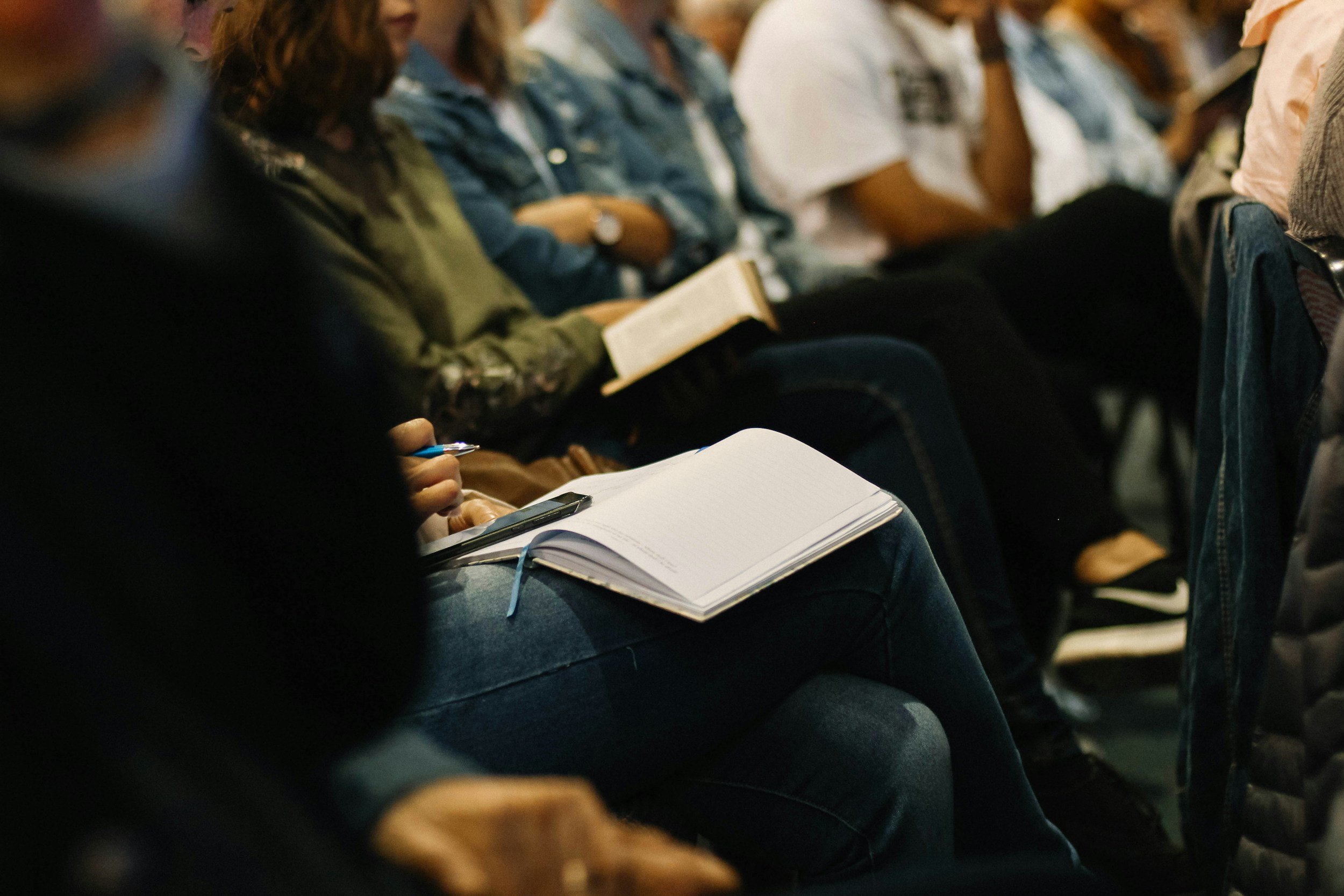
Why our clients love our training:
high quality training workshops designed to be practical, with learning that can be directly applied within the workplace
workshops can be tailored to your sector and specific requirements
facilitated by industry experts
quality course materials; printed in colour on high gsm paper
Kallista Consulting’s network of highly experienced industry professionals develops all of our workshops. They are experienced facilitators with engaging styles who easily command credibility with their audiences.
By incorporating engaging exercise across the duration of each workshop, participants are able to practice the techniques, enabling them to translate the training directly into their workplace to deliver practical outcomes. The materials provided to each participant are comprehensive guides in themselves and include opportunities for participants to record notes and action plans.
Every course can be delivered on-site, remotely via teleconference or through online training platforms and can be customised to provide context within your specific industry and tailored to your desired learning outcomes.
“We were introduced to Chris by a trusted colleague. Chris is a highly knowledgeable consultant who was able to execute needed change in our business at a challenging time. Besides Chris’s knowledge and experience, his greatest attribute was his ability to engage with our team at all levels. He took the time to connect with every member of our team. It was this understanding that built a trust in our team that was the driver for success. I can not recommend Chris highly enough!”
Catherine Hargreaves
General Manager | Hargreaves Joinery
Want to learn more or discuss the course?
We can tailor our workshops to suit your requirements, so if you want the best possible training for your team, why not simply book a time to talk directly with us to talk about your specific training needs.
For a detailed overview and agenda of this workshop, download the Introduction to 5S Training Brochure
Client Partnerships
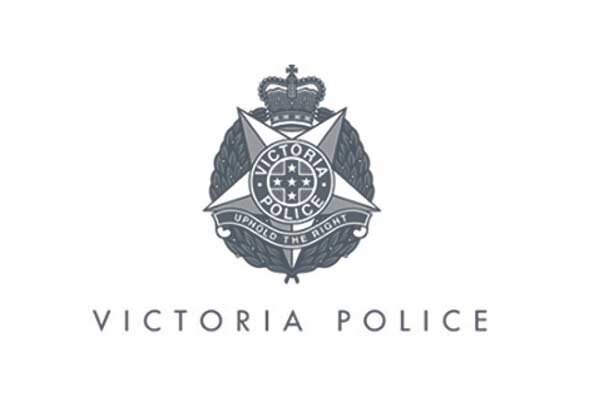
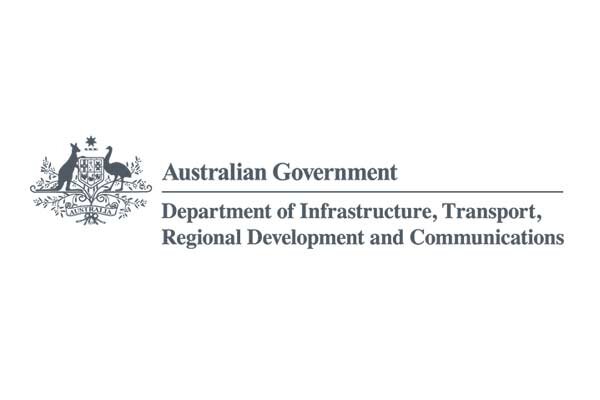

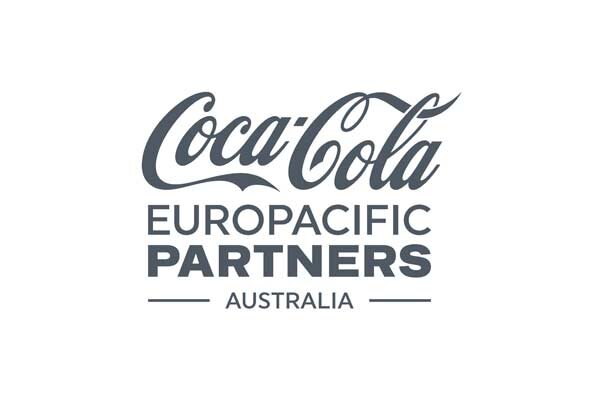
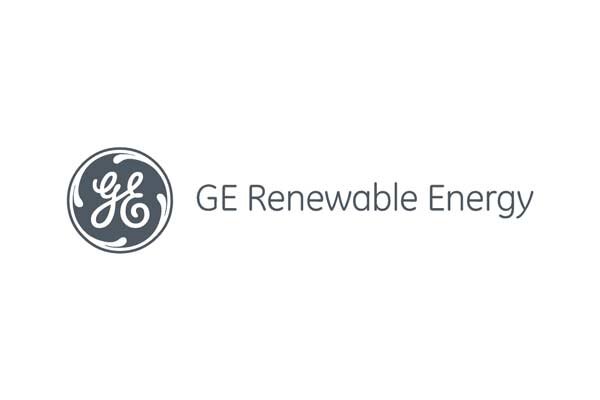
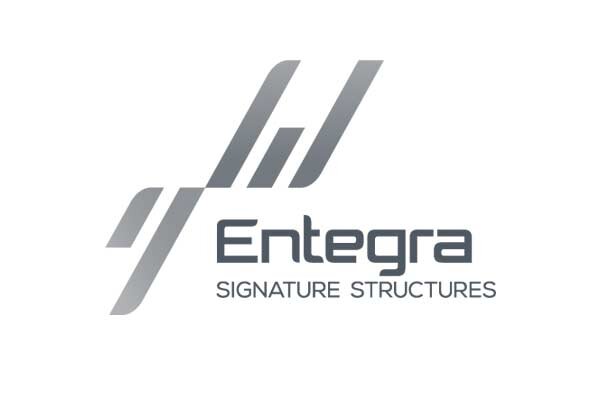
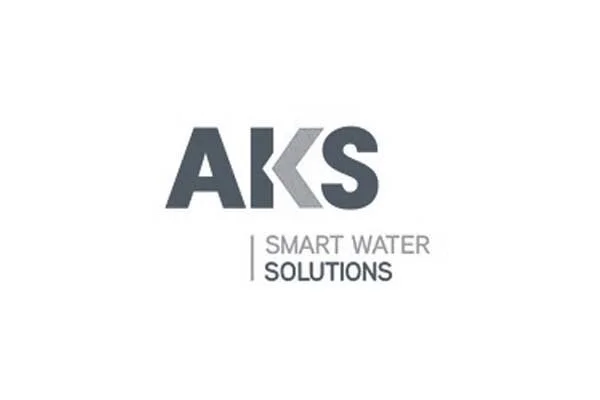
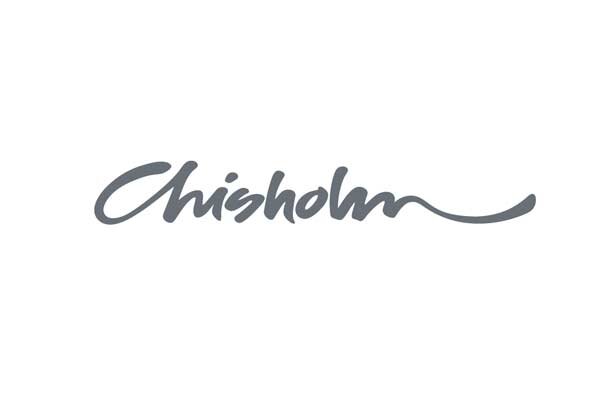
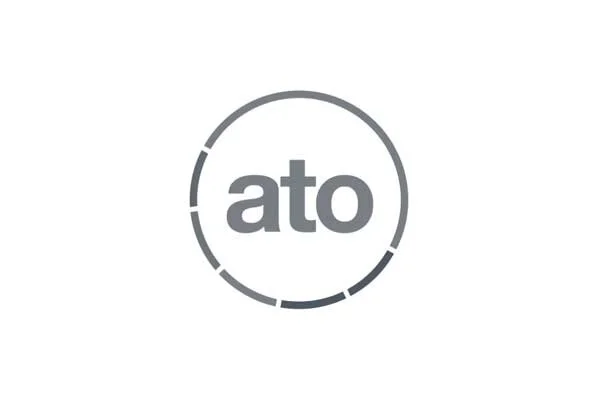
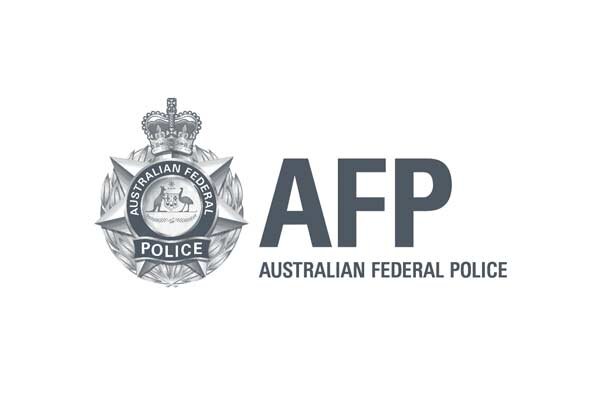

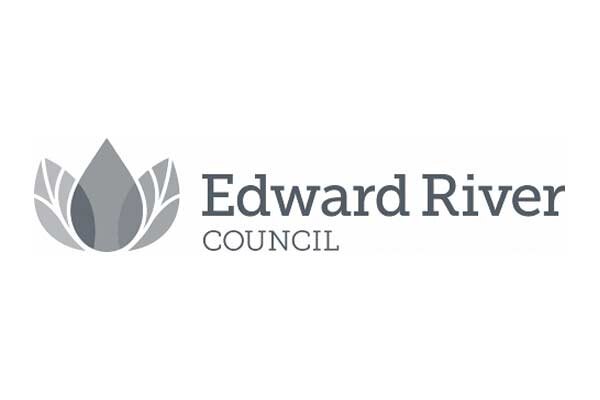