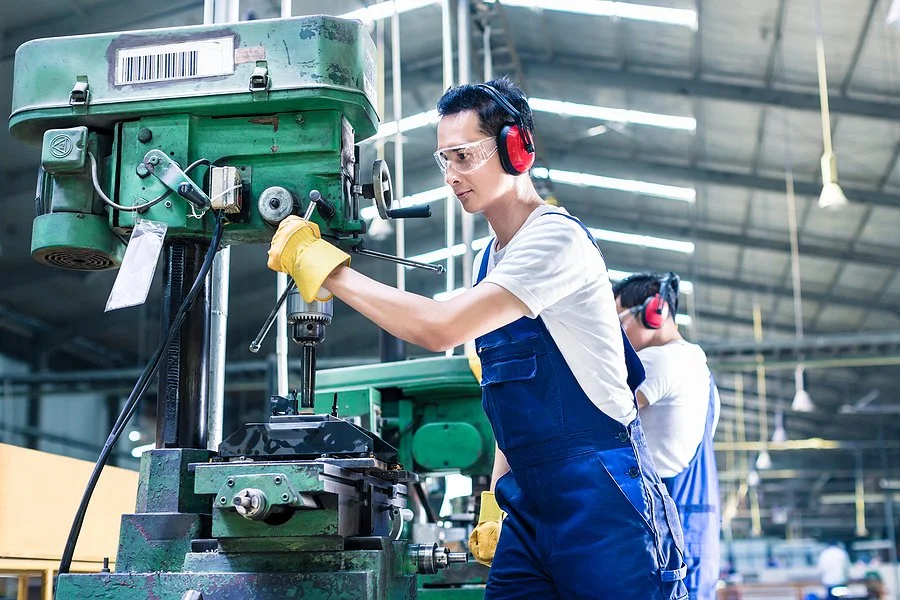
Introduction to Lean for Bespoke Manufacturing
Bespoke manufacturing is a challenging and highly competitive sector, and it has never been more important to understand how the fundamentals of lean manufacturing apply to this type of business. This engaging, interactive and highly practical workshop provides the participants with a fundamental knowledge of lean concepts and how to apply them in a practical way within a bespoke manufacturing environment.
About our Lean for Bespoke Manufacturing Training Workshops
In this video, Chris Baker, founder and principal business advisor at Kallista Consulting, talks about how our Lean for Bespoke Manufacturing Training Workshops can be tailored to suit your custom products business.
Need help improving your productivity?
Be recognised for quality?
Continuous improvement in quality is one of the most important benefits of developing a lean culture. When work is done right first time, it leads to significant reduction in waste and improvement in capacity and throughput, driving increased productivity. It also improves your customer relationships, building trust and loyalty.
Deliver in full and on time
Being able to properly understand your capacity and schedule work so that you are confident that you will deliver in full and on time is transformative to the reputation and productivity of your business. Lean manufacturing tools and techniques help to ensure that teams have all they need to complete work without unnecessary and frustrating delays.
Improve team culture and morale
Once a lean culture takes hold, teams gain autonomy and begin to feel empowered to continually improve processes and layout themselves. Having the opportunity to contribute and develop ownership of their workplace drives extremely positive cultural results, reducing staff turnover and increasing job satisfaction.
How we can help
Having completed this course, participants will understand:
How to focus their thinking when examining a process by observing delivery and quality
The concept of Waste versus Value Adding Work
The 5 principles of a lean organisation
The Workcell Rectangle - How the lean principles apply to a workcell
The core elements of a model for a lean organisation
How to create an ordered and structured workplace using the principles of 5S
How to map processes using Value Stream Mapping and why that is important
The importance of quality and how to continuously improve
The Theory of Constraints
How to schedule bespoke work
How to run or participate in a kaizen event
How to run daily toolbox meetings using visual boards
So why not talk to us now so that we can design a program that helps you meet your Introduction to Lean for Bespoke Manufacturing goals ?
What People Are Saying
“I love the flexibility in the approach that Kallista Consulting takes to tailor a program to meet our specific business challenges. In addition, the energy and personal commitment the team takes to deliver the best-in-class learning experience”
Bobby Pavlickovski
Director Operations | Thales Australia
“Having worked with Kallista Consulting for more than 10-years now, Entegra have found Chris an excellent resource to align with for implementing process performance, systems & structure, driving a culture of continuous improvement and developing emerging leaders amongst our organisation.”
Laurie McCalman
Managing Director | Entegra Signature Structures
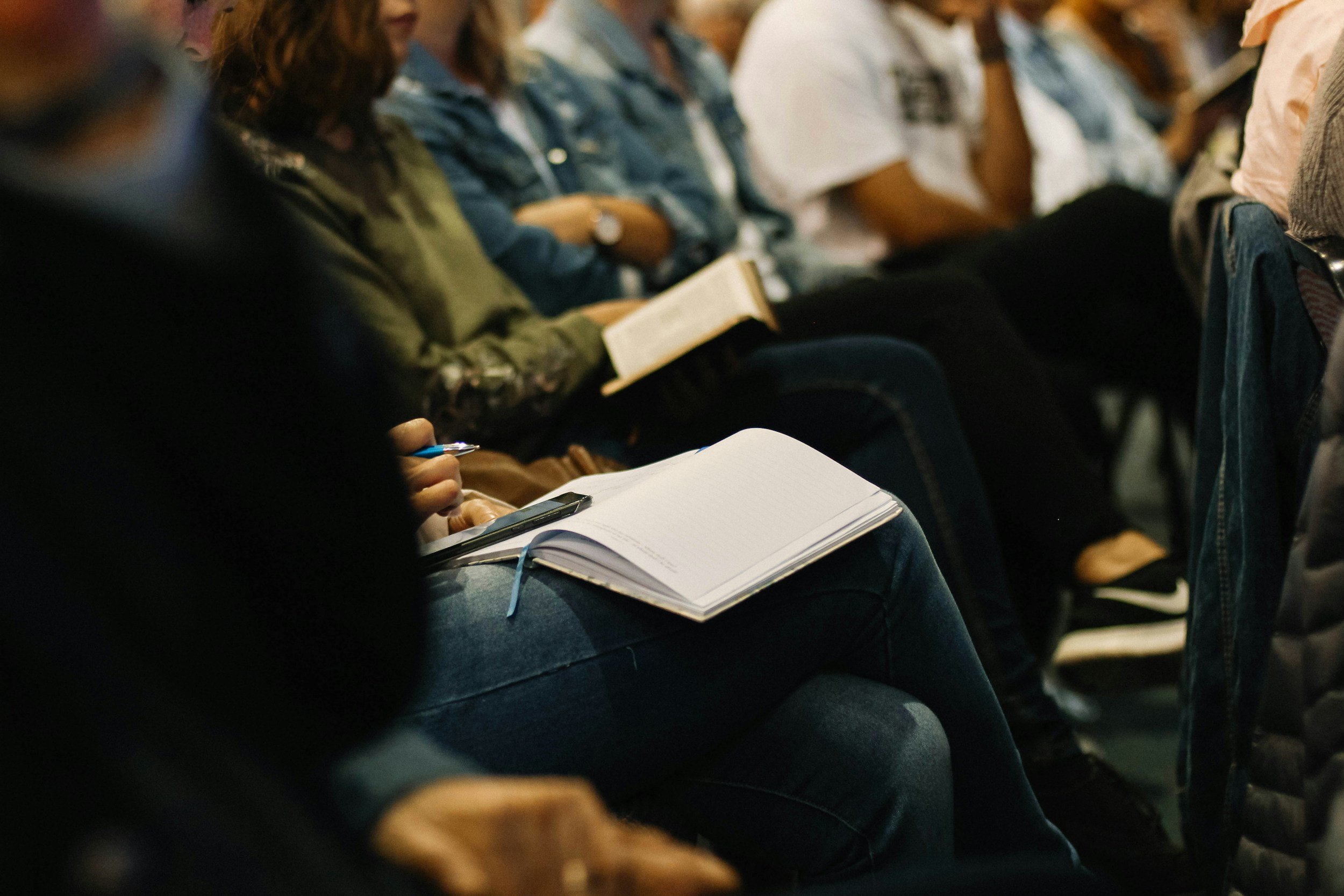
Why our clients love our training:
high quality training workshops designed to be practical, with learning that can be directly applied within the workplace
workshops can be tailored to your sector and specific requirements
facilitated by industry experts
quality course materials; printed in colour on high gsm paper
Kallista Consulting’s network of highly experienced industry professionals develops all of our workshops. They are experienced facilitators with engaging styles who easily command credibility with their audiences.
By incorporating engaging exercise across the duration of each workshop, participants are able to practice the techniques, enabling them to translate the training directly into their workplace to deliver practical outcomes. The materials provided to each participant are comprehensive guides in themselves and include opportunities for participants to record notes and action plans.
Every course can be delivered on-site, remotely via teleconference or through online training platforms and can be customised to provide context within your specific industry and tailored to your desired learning outcomes.
“We were introduced to Chris by a trusted colleague. Chris is a highly knowledgeable consultant who was able to execute needed change in our business at a challenging time. Besides Chris’s knowledge and experience, his greatest attribute was his ability to engage with our team at all levels. He took the time to connect with every member of our team. It was this understanding that built a trust in our team that was the driver for success. I can not recommend Chris highly enough!”
Catherine Hargreaves
General Manager | Hargreaves Joinery
Want to learn more or discuss the course?
We can tailor our workshops to suit your requirements, so if you want the best possible training for your team, why not simply book a time to talk directly with us to talk about your specific training needs.
For a detailed overview and agenda of this workshop, download the Introduction to Lean for Bespoke Manufacturing Training Brochure
Client Partnerships
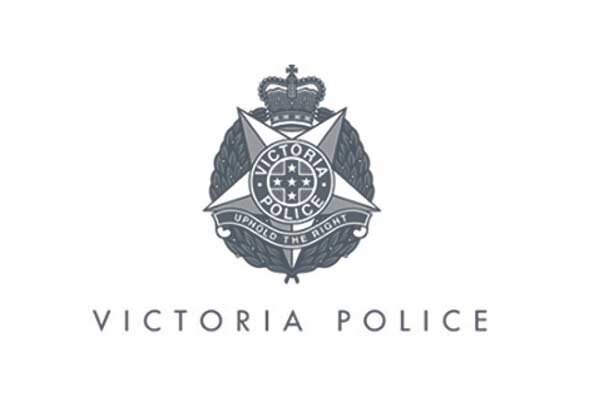
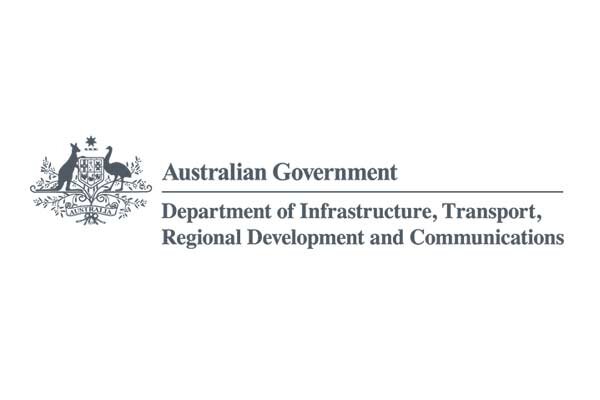

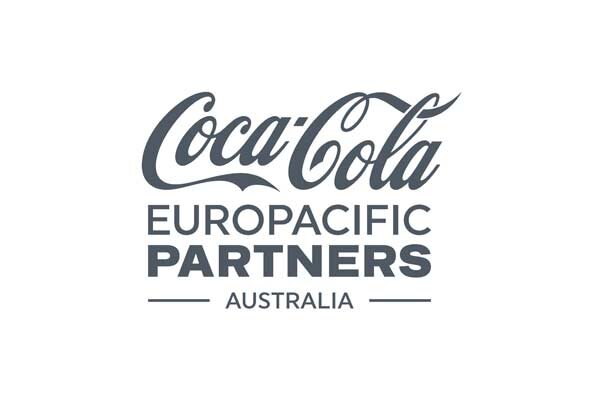
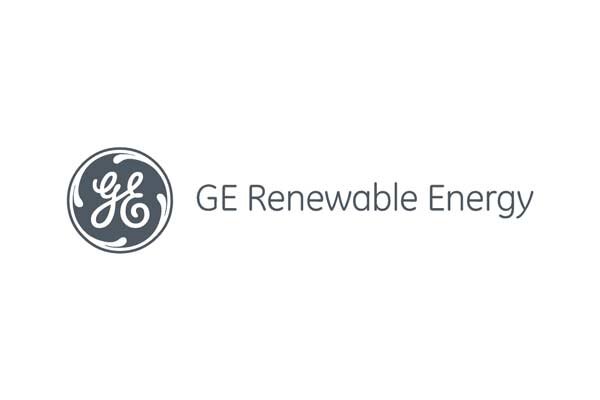
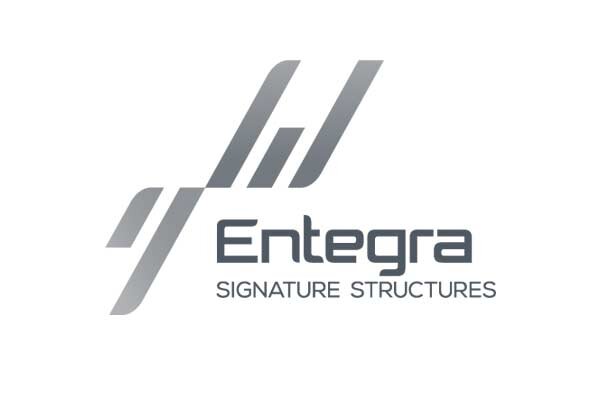
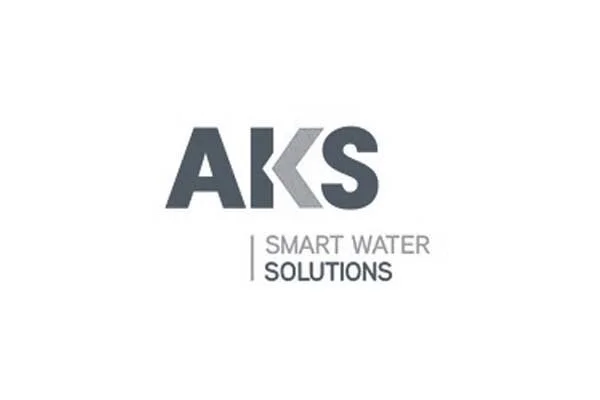
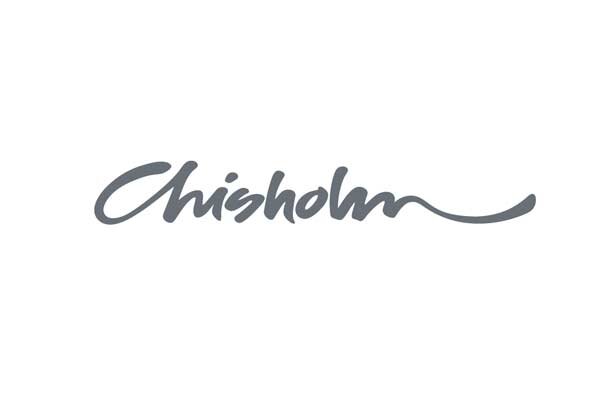
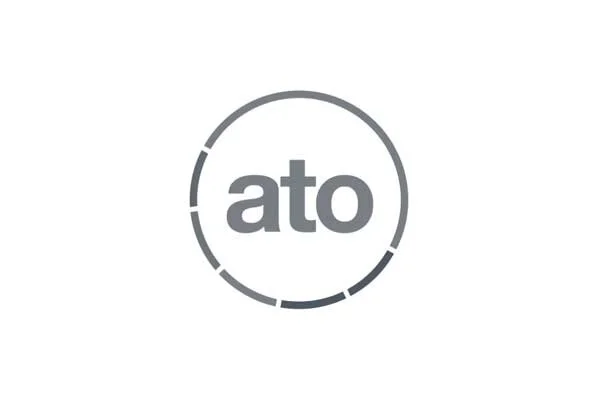
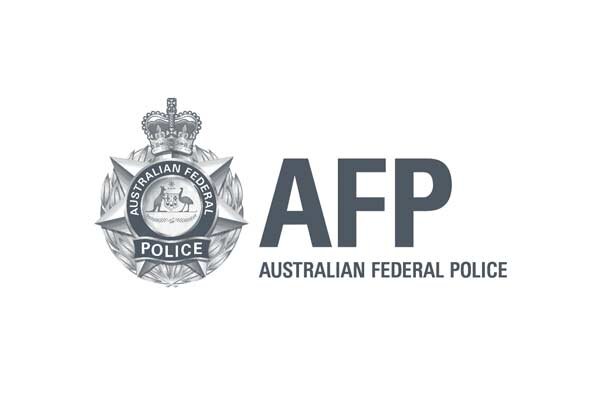

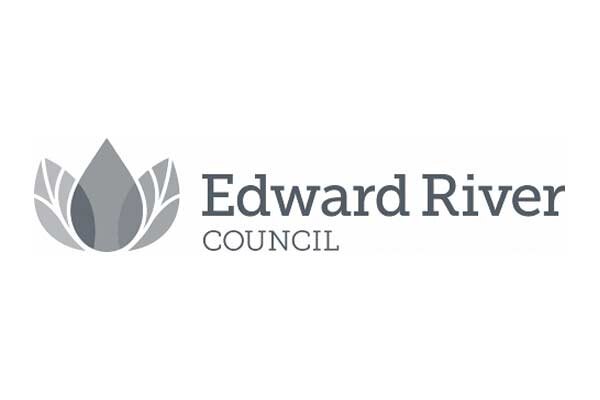